Wheels and Shafts
In making the three-wheel shafts, Fig. 3, 7 and 8, first
drill the bearing-pin holes at the ends of the blocks in perfect alignment
before you do the turning. Slight misalignment can cause binding of pins
in bearing and wobbling of shafts and wheels. The drive-wheel shaft, Fig.
3, has a bearing pin at one end only. The other end rotates in a hole in
the front plate. You drill four pilot holes in this end for brads that
serve as a pinion to turn the hour hand. All the wheels and the ratchet
pulley have 1/2-in. center holes drilled before turning, and these are
used to mount the work on a threaded arbor. One side of each wheel that
can be seen in the assembled clock is turned to a pleasing contour. The
shafts are turned so the wheels fit them snugly. The hole in the ratchet
pulley, Fig. 5, is slightly oversize so it rotates on the shaft. The ratchet
pawl is pivoted on the side of the drive wheel and is kept in firm contact
with the ratchet by a music-wire spring secured by two tiny staples, Figs.
4 and 5.
Cutting the Teeth
The gear teeth can be cut in different ways. One method
consists of laying off the teeth according to dimensions in Figs. 5 and
6, using a sharply pointed hard-lead pencil, or by tracing them from these
drawings. Remove the waste with a fine-tooth handsaw as shown in a photo,
scroll saw, or even a hand fret-saw, and dress down to the marked lines
with a small flat file or manicure sanding stick. Another method involves
the use of a router that slides on a track above the lathe, and an indexing
plate on the lathe spindle having the required number of indexing holes.
Get a restored copy of these Wooden Gear Clock Plans
with 11 Pages of Enhanced and Enlarged Figures and Illustrations
and Searchable Text.
All Orders Processed
On a Secure Server
|
Figure
3 through 5. (3) Drive-Wheel Shaft, (4) Half of Drive Wheel, and (5)
Ratchet and Cord Pulley
|
Matching Wheels to Pinions
Check each shaft separately for easy rotation in the frame
so there is no trace of binding in the bearings. Match the drive wheel
to the 7-tooth pinion on the center-wheel shaft before gluing on the center
wheel. The fit between wheel and pinion will probably be tight so that
the wheel cannot turn freely or at all. Free the teeth by very delicate
dressing, but first blacken with ink the tip of one pinion tooth and the
tips of two-wheel teeth that straddle it when meshing. This assures subsequent
reassembling of pinion and wheel in exactly the same relationship.
To match wheel and pinion teeth, hold the frame in a padded
vise and gently apply a little pressure on the wheel in the same direction
that it will rotate in the clock, at the same time putting a slight drag
on the pinion to simulate actual working stresses. Carefully determine
just where binding occurs both when a pinion tooth starts to engage the
wheel teeth and when it disengages from them. A small piece of carbon paper
fed between the meshing teeth will show up points of excessive rubbing.
Dress only the slopes of the wheel teeth but not the tips
as this reduces the wheel diameter. Too much dressing ruins a wheel because
it produces excessive clearance and allows pinion teeth to strike the tips
of wheel teeth. Remove all high spots from the wheel teeth that tend to
slow rotation of the wheel when it is barely touched with your finger and
the pinion is kept under a slight drag. The tips of pinion teeth should
be semicircular in cross section and must not be dressed down on the top.
If the tips of the wheel teeth bind on the bottom of pinion gullets, deepen
them a trifle. After matching the drive wheel to the pinion on the center-wheel
shaft, glue the center wheel to its shaft and proceed to match it to the
pinion on the escapement-wheel shaft. This is done while the drive wheel
is removed. |
|
Figures 6 though 10. (6) Half Center Wheel.
(7) Center Wheel Shaft,(8) Escapement Wheel and Shaft, (9) Hand Wheel,
and (10) Hand
|
Escapement Mechanism and Timing
Drill pilot holes for the equidistant brads of the escapement
wheel, Fig. 8. using glue on the brads for extra holding power. Uniform
height is obtained by grinding. Fig. 11 shows the rocker arm and associated
parts. Sheet-metal retents on the shaft alternately stop the escapement
wheel momentarily. Just before an obstructed pin is freed from one retent
the opposite one swings in to obstruct the pin moving toward it. Bend the
retents separately to proper shape on a nail of the same diameter as the
shaft, then slip them on the shaft and solder in place. Inside surfaces
of retents should be very smooth. After pressing the rocker arm on the
shaft, you can "snake" the latter into position down through the hole in
the upper crosspiece. When the shaft is set in its bearings and hangs from
the top pin by thread, the relents should swing about halfway over the
pins when engaging them. Adjust for this distance by moving the bearings.
Avoid contact of the shaft against the bearing pin of the escapement wheel. |
|
Waste between the teeth is first removed
with band, or scroll Saw, then filed to the line with a small flat file.
|
|
The escapement mechanism will require delicate adjusting,
mostly by bending the retents in or out. If spread apart too far they won't
stop wheel rotation. If a retent lands and stops on the tip of a pin, the
spread must be decreased slightly. When the retents are too close the pins
cannot pass either of them.
Two 1/2-oz. weights on the rocker arm can be shifted to
adjust timing. If this is not enough the rocker-arm weights are made lighter
for faster movement and heavier for slower movement. Fig. 12 details the
weight pulleys and cord. The latter goes through the anchor posts and is
knotted above each. If the cord slips on the ratchet pulley apply some
rosin. The pulleys must not bind in the sheaves, which may be enough to
stop clock movement. The 3 oz. weight serves only to keep the cord taut. |
|
Figure 11. Rocker Arm and Fittings.
|
|
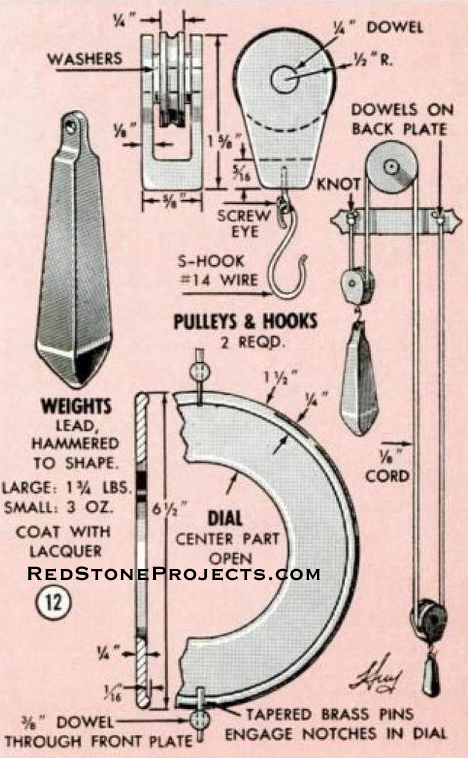 |
Figure 12. Weights, Pulleys, and Hooks.
|
Hour Wheel and Dial
The hour wheel is identical to the center wheel but is
glued to a sleeve, Fig. 9, which fits the dowel on the front plate. Fig.
10 shows the hand which is easy to loosen and tighten for changing its
position. A tapered brass pin slips through the dowel. The dial, also shown
in Fig. 12, surrounds the hour wheel and is held by tapered brass pins
which also hold the front plate on the crosspieces. Numerals on the dial
can be done with India ink later covered with transparent lacquer. The
clock pictured here is a replica of one of the first hand-made, weight-operated
clocks. Making a copy of it will increase your admiration of bygone craftsmen.
The closeup view minus the dial, hour wheel and hand, shows the relationship
of the three time-keeping wheels and the escapement mechanism. These took
great skill to form before the advent of precision power tools. |
|
Wooden Clock Numerals
|
|