Free Shipping on All U.S. Orders
All Orders Processed on a Secure Server
Build This Tent On Wheels Folding Trailer
Build Your Own Folding Trailer Plans
|
Vintage Tent On Wheels Folding Trailer Plans
Build Your Own Pop Up
Camping Trailer
 |
PDF Format |
|
All Orders Processed
On a Secure Server
|
Price $12.95
|
Get a restored copy of these vintage Tent On Wheels
Folding Camper Trailer Plans with 22 Pages of Enhanced and Enlarged
Figures and Illustrations and Searchable Text.
|
We will email these plans, to the address provided
with your payment, within 48 hours following receipt of your order.
|
|More
Vintage Trailer Plans|
|
|
 
|
 
|
|
PART 1
Like so many outdoor loving people my family thoroughly
enjoys spending its vacations and long weekends camping out, roughing it,
so to speak, while exploring the many lakes and back trails of this great
U.S.A. After having roughed it several summers in true Boy Scout style,
we decided to design and build a camping trailer that would incorporate
"all the comforts of home" in a compact, two-wheel job capable of being
trailed safely at highway speeds.
Having two boys, Bruce and Craig, I knew that the trailer
would have to sleep at least four, it would have to be small enough to
park in my two-car garage, and it would need a roomy ice chest to handle
an ample food supply. It also would have to afford adequate protection
in bad weather and, preferably, be collapsible, which meant finding a way
of erecting and dismantling it without a lot of work. In short, a fold
away "tent" on wheels was what we needed.
The trailer you see pictured below fulfills all these
requirements. And, after having put It through a tour of the West last
summer (a grueling test of some 5000 miles), we found the trailer towed
beautifully, provided all the comforts we had hoped for and caused a mild
sensation wherever we set up camp or pulled stakes.
When open, each overhanging wing of the trailer to which
the tent is permanently attached, accommodates a full-size air mattress
to provide comfortable sleeping for four. The deep insulated ice chest
at the front of the trailer is easy to reach both when the trailer is open
or closed. The boys found this feature especially convenient for getting
Cokes and other treats while on the road. Likewise, two lock fitted compartments
in the nose of the trailer permit quick access to Items that might be needed
enroute without opening the trailer itself. Two persons can easily erect
the canvas top in a few minutes, and a full-length screen door keeps flies
and mosquitoes outside. The center portion of the trailer interior affords
space to store an aluminum table and chair set, as well as a camp stove.
The screen door stows away in a trap door in the floor, and built-in compartments
with sliding doors provide plenty of room for cooking utensils, bedding
and clothing.
Down to the last nut and bolt, the trailer cost me $457.31
to build. However, we later found we could have saved as much as $30 on
the cost of the canvas top ($133) by having the awning makers sew it together
during their slack season. If materials can be salvaged and a second-hand
running gear purchased, the cost can be reduced considerably. |
|
Independent of motel and restaurant, the Kendall
family are enjoying camp life at it's best with this trailer.
|
I made the bed of the trailer body from lengths of 3
in. channel iron and 1 in. angle iron, and welded the 18 separate pieces
into a rigid framework. The channel stock is used for the main members
of the bed and the tongue. these parts being shaded in the plan drawing,
Fig. 5. Note that the forward ends of the two center members are cut at
a 13-degree angle to match the slant of the two front members of the bed.
I laid out the members squarely on my garage floor to assure a flat assembly
when welding the joints. The various members are placed in position, with
the flat side of the channel facing outward. The two center channels are
spaced 36 in. apart and butt welded to the front and rear members. Two
short lengths of channel, 16 3/4 in. long, are butt welded to the center
members on each side of the bed to form the wheel wells.
Three pieces of angle iron, marked A on the drawing, are
cut 39 in. long and welded to the underside of the two center channels.
These pieces provide support for a 3/8 in. plywood floor. Lengths of angle
iron also are welded along the center channels and along the outer edges
of the bed at the sides as indicated in section B-B, Fig. 5.
You can use any suitable two-wheel running gear, Fig.
4. I purchased a 58 in., drop axle type having 16 in. wheels from Montgomery
Ward for about $60. Spring mounting plates, 3/8 x 6 x 8 in., are welded
to the bed on the underside at the points shown and drilled for the shackle
bolts.
The locations of the angle iron posts to which the sides
of the body are bolted, are spotted on the plan drawing. These are cut
from 1 in. angle iron. A total of 24 are needed, ten of these being 27
in. long, two 29 in. long and twelve 14 in. long, the latter ones being
located at the wheel wells, B in Fig. 5. All posts are merely butt welded
on end at their respective locations. If you study the plan carefully,
you can see the way each post faces. Holes for bolting the plywood sides
to the posts should be spot ted and drilled before the posts are welded
in place. Drill six holes for 5/16. X 1 1/4 in. carriage bolts in
each 27 in. post, spacing them about 5 in. apart. |
Get a restored copy of these vintage Tent On Wheels
Folding Camper Trailer Plans with 22 Pages of Enhanced and Enlarged
Figures and Illustrations and Searchable Text.
All Orders Processed
On a Secure Server
|
Figures
1 and 2.
Tent on Wheels side panels, front bulkhead dimensions
and construction details.
|
The two 29 in. posts are butt welded to the edge of the
1 in. angles along the sides 13 5/8 in. back from the front corner posts.
These particular posts support the plywood bulkhead, marked X in Fig. 10.
Note that this piece is rabbeted along the top edge to engage a groove
on the underside of each trailer lid to give a watertight joint. Looking
at the end view, Fig. 5, you'll notice that the 1 in. posts at the rear
door opening have a second post of 1 1/2 in. angle iron welded to them.
These are set in 3/4 in. and provide a bolting surface for attaching the
frame of the screen door to be described later. Finally, lengths of 1 in.
angle Iron are welded across the tops of the |
|
Pipe extensions are screwed on lid
supports to increase their length.
|
|
Figure 3. Thin-walled conduit tent frame and mounting
details.
|
|
Bolt-head studs project from lids to
engage ends of pipe supports.
|
|
Figure 4. Tent on Wheels suspension and running
gear.
|
|
Trailer body framing.
|
14 in. posts and between the posts at the rear of the
bed. Study section A-A, Fig. 5, and the end view. These members form a
shelf on each side which is covered with hardboard.
The outside is covered with 3/4 in. marine plywood. Figs.
1, 8 and 10 give the sizes for the various panels. Exact lengths should
be taken directly from the trailer bed, adding 3/4 in. to the length of
the side panels to lap the plywood applied to the back. Before the side
panels are permanently bolted in place, the wheel wells first are lined
with plywood and then fitted with a sheet metal liner. This is soldered
and riveted as in Fig. 2, the cut-out edge being serrated to form tabs
for nailing the liner to the edge of the plywood side panel.
Figs. 6 and 7 detail the ice chest and its cover. You'll
notice that the plywood part of the cover is rabbeted around the edges
to bear against a length of sponge rubber weather stripping applied around
the opening in the bulkhead cover board. Standard ice chest hardware is
used to hinge the cover and provide a positive seal. The ice chest itself
hangs in the opening by flanges, and glass wool insulation is packed solidly
around it.
The lids, or doors, which overhang the sides when the
trailer is open, are hinged with lengths of 4 in. continuous hinge which
I bent in a sheet metal brake, as indicated in Fig. 9. I could buy this
hinge only in 6 ft. lengths so I made up the difference by adding a section
to it. Fig. 3 shows how the pipe supports for the lids are installed. These
pivot in brackets located in the wheel wells and swing up from spring clamps
to engage bolt head studs projecting from the top surface of the lids.
Pipe extensions are stowed separately. |
Get a restored copy of these vintage Tent On Wheels
Folding Camper Trailer Plans with 22 Pages of Enhanced and Enlarged
Figures and Illustrations and Searchable Text.
All Orders Processed
On a Secure Server
|
Figure
5. Tent on Wheels trailer chassis and frame dimensions and construction
details.
|
|
Figure 6. Trailer ice chest dimensions and construction
details.
|
|
Figure 7. Ice chest lid dimensions and construction
details.
|
|
Weather stripping provides a seal for ice-box
cover.
|
|
Figure 8. Tent Trailer aft bulkhead and door dimensions
and layout.
|
Get a restored copy of these vintage Tent On Wheels
Folding Camper Trailer Plans with 22 Pages of Enhanced and Enlarged
Figures and Illustrations and Searchable Text.
All Orders Processed
On a Secure Server
|
Figures
9 and 10.
Tent trailer body construction detailing fold out
beds.
|
|
I used an Atwood commercial hitch that bolt to
the channel-iron tongue. Hitch permits easy rolling.
|
|
Atwood trailer hitch.
|
|
Compact as it is, Kendall's trailer has room for
stowing table-and-chair set, stove and cooking utensils.
|
EDITOR'S NOTE: In part I, Jim Kendall explained
how the bed and body of his trailer were welded together from channel and
angle iron, how the ice chest was installed and how marine plywood was
used to cover the outside. Part II concludes instructions for completing
Kendall's "tent on wheels."
|
With construction completed to the point discussed last
month, your next step is to add the framework to the underside of the trailer
lids. This framework serves primarily as an anchor point to which the tent
is permanently attached along each side.
In studying Fig. 12, you'll notice that the framework
consists of box channel on three sides over which tempered hardboard is
applied and supported every 6 in. by wooden cleats. I made the box channel
by placing two lengths of 1 in. angle iron together as shown and welding
them along the edges at intervals of 6 to 8 in. The channel is bolted to
the plywood lids ap proximately 1 1/4 in. in from the edge all around,
using 1/4 in. carriage bolts long enough to also pass through the hardboard
covering. Holes spaced about 8 in. apart are drilled and tapped in the
outer faces of the box channel. These receive small machine screws which
are used to fasten flat iron, canvas clamping strips to the channel. Flat
headed 1 1/4 in. wood screws are used to fasten the hard board to the cleats
and the cleats to the plywood trailer lids. |
|
Figures 11 and 12. Tent trailer folding
cover construction and attachment details.
|
|
To set up camp, wings of the trailer to which
the
tent is attached are First opened outward and
supported by fold-away pipe braces.
|
|
|
Pipe framework swing upward from the
trailer body to support tent roof like Covered
wagon. Steps under body keep trailer from tipping.
|
|
Jim Kendall buttons canvas to row of regular curtain
fasteners which are added to the front of the trailer.
|
With this step completed, you can turn to making the
two folding platforms which are used to increase the width of the trailer
lids so that standard 54 in. air mattresses can be used. Fig. 13 details
the construction of the platforms and shows how they rest on the built-in
seats when in use. They are made of 3/4 in. plywood and have three legs
which are hinged to fold flat. Note that the top board overhangs at the
rear so it can rest on the trailer lid and be flush with the hardboard.
A suitable groove is run on the underside of the overhang to allow it to
fit over the barrel of the continuous hinge supporting the lid. Over all
measurements of the platforms should allow clearance for the lugs to which
the tent bracing is pivoted. The links which hold the legs open are made
from short lengths of flat metal. When folded flat, the platforms are stowed
on the seats. In rainy weather this makes it possible to still use the
seats when eating inside the trailer.
Space under the seats on each side of the wheel wells
is converted to storage compartments with sliding doors of tempered hardboard.
The cross-section view in Fig. 15 shows how tracks are made for the sliding
doors. The upper track is formed by a rabbeted strip which is bolted to
the face of the angle iron seat rail, flush with the top. The lower track
is formed by two 1/4 in. cleats nailed to a 3/4 x 2 1/4 in. strip which
is bolted to a channel member of the trailer bed. The 1 1/4 in. cleats
are lined up, of course, with the rabbet directly above. The 3/8 in. rabbet
allows ample clearance for the two sliding doors so that any subsequent
swelling will not cause them to bind. Handles are formed by boring a 1
in. finger hole in opposite ends of the hardboard panels. Stops for the
hinged trap door in the floor, which affords access to a storage well below
it, are bolted to the underside of the wooden channel strips. The stops
run the full length of the door and you'll note that one edge of each one
is rabbeted to fit over the edge of the iron channel. The trap door itself,
below which the screen door is stored, is hinged along one side, the hinges
being set flush so they will not interfere with the hard board sliding
doors. The trap door should be short enough to allow the screen door to
rest directly on the channel iron of trailer bed when the door is set up.
A hand hold is cut in the lower left-hand corner of the door for easy lifting.
I made the screen door in one piece as you can see in
the photo on the opposite page, although I since have converted it into
a Dutch type door as detailed in Fig. 14. This proved more convenient in
that the door of the trailer itself could be closed and yet allow the upper
part of the screen door to be opened independent of the lower section.
The 3-piece frame for the door is made of 3/4 x 3 in. hardwood. I used
mortise and tenon joints at |
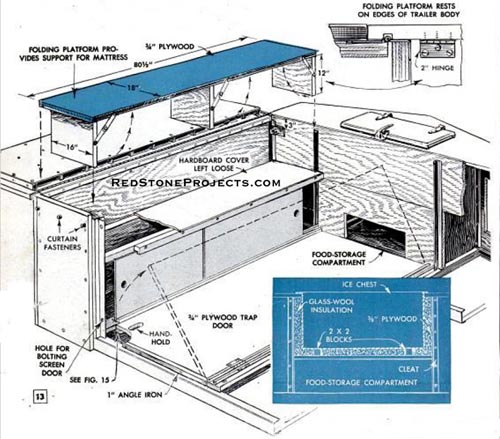 |
Figure 13. Tent trailer folding platform construction.
|
the upper corners and braced them on each side with flat
iron mending plates. These corners could be doweled or held with corrugated
fasteners. The doorframe is braced across the bottom with a flat iron strip
which I bent at right angles to extend up the sides of the frame, flush.
Note that the upper section of the screen door is fitted with regular curtain
fasteners to permit buttoning a canvas flap across the top. Curtain fasteners
also are added to the doorframe, one on each side, in line with those previously
added to the trailer body for buttoning the tent top. The screen door unit,
which is installed after the tent top is erected, is held securely by four
flat headed |
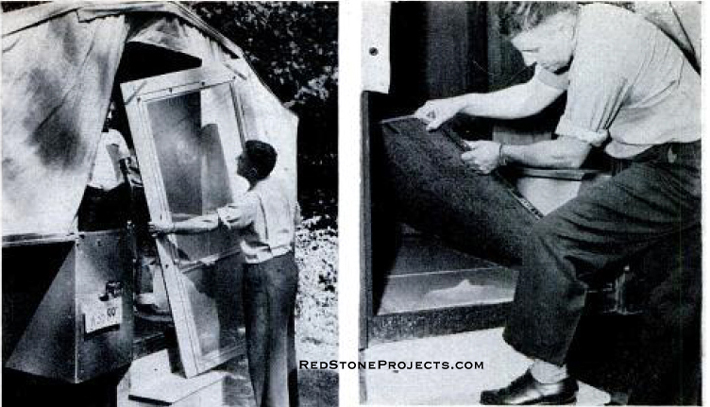 |
Screen door unit bolts to door opening and tent
flaps button to doorframe. Screen door unit stores in well under
trap door in trailer floor.
|
|
Fig 14. Tent trailer sreen door dimensions and
construction.
|
stove bolts fitted with wing nuts. Holes for these are
made in the doorframe to correspond with the holes previously drilled in
the angle iron pieces to which the frame is bolted. The top view detail
in Fig. 14 shows the wing nuts on the inside so they will not interfere
with closing the trailer door. The handle for the screen door is attached
to the upper section so it clears the trailer door when the latter is closed. |
|
Figure 15. Tent trailer storage compartments and
sliding doors.
|
Fig. 11 shows how I sealed the two access doors in the
nose of the trailer with sponge rubber to make the storage compartments
dust and water tight. Rabbeted edges around both door and door opening
provide space for the rubber which is cemented to the cleats that form
the inner rabbet. In closing, the door compresses the sponge rubber and
seals the joint tightly.
This brings you to the tent and its supporting pipe framework.
Except for the two main units of the framework which are shown red in Fig.
16 and which are permanently attached to the trailer body, all supporting
members are designed to come apart to facilitate storing. The two main
units are pivoted in welded angle iron brackets bolted to the trailer body
and fold flat. You'll notice here that height adjustment is provided to
take up any slack in the canvas. I made the whole framework of rigid and
thin wall electrical conduit. The bows which stretch the sides of the tent,
are fitted with pins in the ends to engage holes in the lower ends of the
main supporting bows. Note that these side bows are made to come apart
in three pieces. Pipe X serves as a prop to support the one-piece front
bow. The lower end sets over a bolt head stud in the trailer body, while
the upper end has a pin to pass through a hole at the mitered joint.
In erecting the tent top, the main bows are swung up in
position first, and then the three stretcher pipes are put in place over
welded studs. Usually, there is enough play in the canvas top to permit
the stretchers to be forced |
|
Set up tent trailer with open door and hanging
lantern.
|
|
Drop curtain tent window, which any awning maker
can add, is installed on each side of the trailer.
|
Get a restored copy of these vintage Tent On Wheels
Folding Camper Trailer Plans with 22 Pages of Enhanced and Enlarged
Figures and Illustrations and Searchable Text.
All Orders Processed
On a Secure Server
|
Tent
trailer folding frame details and tent pattern with dimensions.
|
over the studs. Exact lengths of the various members
that make up the framework are best determined from the actual tent itself
as the overall size of the tent will vary somewhat in each individual case.
Patterns for the tent accompany Fig. 16. I had this sewed
together by an awning maker and suggest that you do, too. They know how
to add the drop curtain windows and are equipped to install the grommets
for buttoning the tent to the trailer. The 3 in. flap indicated across
the top of the rear pattern is optional. I had this sewed in at the |
|
Lock fitted, rubber sealed doors to
storage compartments in nose
of trailer are hinged with piano hinges.
|
time, as I plan to add a canvas canopy, supported by
tent poles. over the door. The flap will provide a means of buttoning the
canopy. |
Any 2 Vintage Trailer Plans
$19.95 FREE Shipping |
Select 2 Vintage Travel Trailer Plans
|
|
|